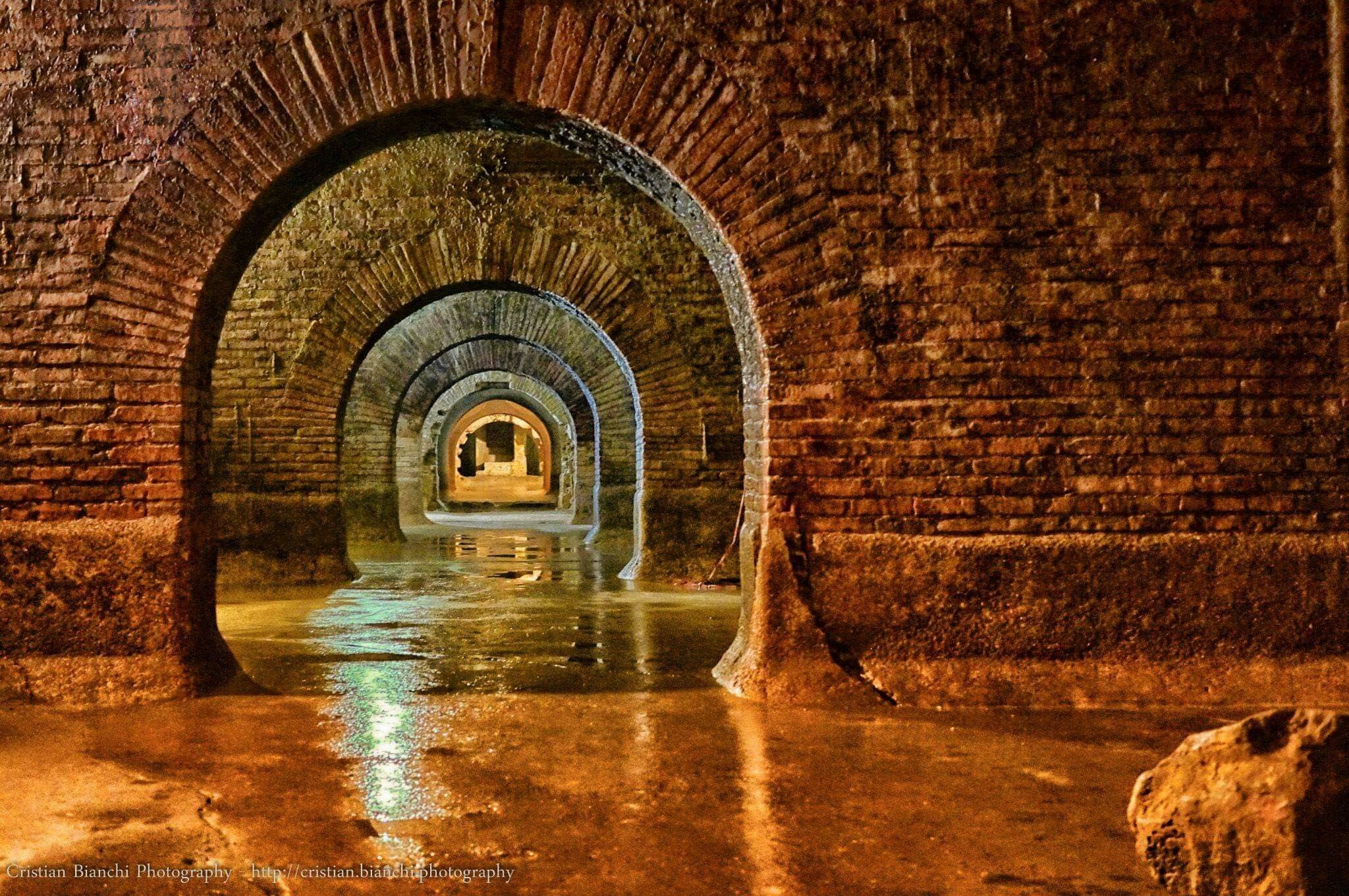
Architect Philip Frohman, built over 50 churches and cathedrals in the United States until his death in 1972. These range from the grand Washington National Cathedral and to a much smaller project, the Church of the Heavenly Rest in Abilene, Texas. While in the early budget and planning stages of the Abilene project Philip asked the building committee, “What do you want to build? A church to last 100 years or 500 years?” I heard this story while being given a tour of the church in Abilene a good twenty years ago. My tour guide told me the building committee chose 500 years which meant it would take a lot of time and money to build, a considerable investment in the future. The question, “What do you want to build?” became in my mind, a metaphor for not just for how long something lasts but legacy.
This week I toured an ancient public work in Fermo, Italy, The Roman Cisterns. Emperor Augustus commissioned this tremendous engineering project in the first century B.C. He intended the water system to provide drinking water for the Roman colony of Firmum Picenum (now Fermo) on Italy’s Adriatic coast. The water was collected from natural springs and rain. Deep under the city’s tufa rock, the engineers built a complex arrangement of graded cisterns and aeration to purify and store water. Some historians believe the system was also used to pipe water to Roman expeditionary ships in the nearby harbor of Porto San Giorgio.
When the Roman Empire fell, the cisterns were “forgotten.” In the 13th century, Dominican monks stumbled upon the underground caverns while building a new monastery. The monks used part of this system for their winery, and you can still see the stairway and barrel chutes they built from their monastery to store wines. There remain two great concrete fermenting tanks.
It is difficult to believe that such a structure was built 2000 years ago. Imprints of the forming boards used to make ceilings, the cleaning platforms, aeration wells, brick walls remain in relative good condition. The bricks look good as new. It is in such great condition that post WW2 Fermo used it for a holding tank for city water.
The system covers more than 21,000 square feet and consists of 30 interconnected tanks in three rows of 10 chambers. Each tank is slightly lower than the next, allowing water to flow slowly from one cistern to another. Water levels were kept at about 28 inches to allow the slow aerating movement of the water from tank to tank, and so sediment could fall to the bottom of successive tanks. Ventilation came from 10 shafts that opened periodically to allow air to circulate in the underground chambers.
The longevity of Roman concrete has been in the news lately. Youtubers have produced videos about how to DIY and universities have devoted research to the mystery. The ancient Romans were master engineers.
Rome’s Pantheon, which has the world’s largest unreinforced concrete dome, dedicated in A.D. 128, is still intact, and some ancient Roman aqueducts still deliver water to Rome today. Meanwhile, many modern concrete structures have crumbled after a few decades. Do you hear me Frank Lloyd Wright?
A team of investigators from MIT, Harvard University, and laboratories in Italy and Switzerland, has made progress in this field, reverse engineering ancient concrete-manufacturing strategies that incorporated several key self-healing functionalities. The findings <https://www.science.org/doi/10.1126/sciadv.add1602> are published January 6, 2023 in the journal Science Advances, in a paper by MIT professor of civil and environmental engineering Admir Masic, former doctoral student Linda Seymour ’14, PhD ’21, and four others.
Historically, it had been assumed that when lime was incorporated into Roman concrete, it was first combined with water to form a highly reactive paste-like material, in a process known as slaking. One Youtuber demonstrates this process but I recommend against following his example because he didn’t wear gloves and you can get quite a lime burn by direct skin exposure. However this process alone could not account for the presence of the lime clasts. Masic wondered: “Was it possible that the Romans might have actually directly used lime in its more reactive form, known as quicklime?”
Studying samples of this ancient concrete, he and his team determined that the white inclusions were, indeed, made out of various forms of calcium carbonate. And spectroscopic examination provided clues that these had been formed at extreme temperatures, as would be expected from the exothermic reaction produced by using quicklime instead of, or in addition to, the slaked lime in the mixture. Hot mixing, the team has now concluded, was actually the key to the super-durable nature.
“The benefits of hot mixing are twofold,” Masic says. “First, when the overall concrete is heated to high temperatures, it allows chemistries that are not possible if you only used slaked lime, producing high-temperature-associated compounds that would not otherwise form.
Second, this increased temperature significantly reduces curing and setting times since all the reactions are accelerated, allowing for much faster construction.”
During the hot mixing process, the lime clasts develop a characteristically brittle nanoparticulate architecture, creating an easily fractured and reactive calcium source, which, as the team proposed, could provide a critical self-healing functionality. As soon as tiny cracks start to form within the concrete, they can preferentially travel through the high-surface-area lime clasts. This material can then react with water, creating a calcium-saturated solution, which can recrystallize as calcium carbonate and quickly fill the crack, or react with pozzolanic materials to further strengthen the composite material. These reactions take place spontaneously and therefore automatically heal the cracks before they spread. Previous support for this hypothesis was found through the examination of other Roman concrete samples that exhibited calcite-filled cracks.
To prove that this was indeed the mechanism responsible for the durability of the Roman concrete, the team produced samples of hot-mixed concrete that incorporated both ancient and modern formulations, deliberately cracked them, and then ran water through the cracks. Sure enough: Within two weeks the cracks had completely healed and the water could no longer flow. An identical chunk of concrete made without quicklime never healed, and the water just kept flowing through the sample. As a result of these successful tests, the team is working to commercialize this modified cement material.
So mystery of Roman concrete is solved, another question is how did they remove all that material without heavy equipment? Very large and heavy buildings are hundreds of feet above the cisterns. The reality is that the cisterns were built into the side of the hill. Over 2000 years the cisterns became buried by centuries of human detritus and buildings. It took 1300 years for our friends the Dominican monks to discover what lay beneath their monastery and turn it into a winery. I still have questions. One of which is what kind of society and leadership can conceive of, plan and execute civic projects of this scale. Rome came, it saw, it conquered then…. it fell… yet it’s structures remain 2000 years later?
[Story written by Mary Stanley of Brownwood as she chronicles her travels through Italy]